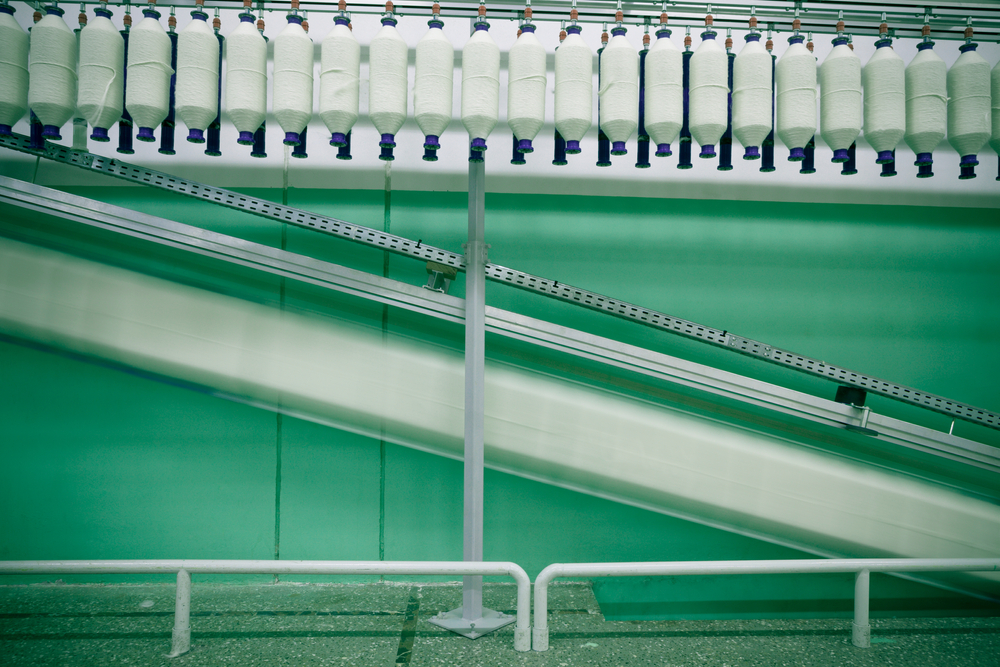
Improving Safety Standards with Reliable Conveyor Components
May 1, 2024 9:17 pm Leave your thoughtsConveyor systems play a crucial role in the manufacturing industry, especially in environments such as cotton mills and gins where the handling of materials is constant and demanding. These systems rely on various components to ensure smooth and efficient operation, but it is important to prioritize safety when it comes to the maintenance and upkeep of conveyor components. In this blog post, we will discuss the best tips and practices for conveyor component safety, focusing on how reliable components can help improve safety standards in environments like cotton mills and gins.
Understanding the Importance of Conveyor Component Safety
Conveyor systems in cotton mills and gins are responsible for moving large volumes of materials such as cotton bales, seeds, and fibers from one location to another. The use of conveyor systems can significantly increase productivity and efficiency in these facilities. However, the operation of conveyor systems also comes with inherent risks, especially when it comes to the safety of workers who are in close proximity to moving parts and components.
Tips for Warehouse Safety
1. Regular Maintenance and Inspections: One of the best ways to ensure conveyor component safety is to conduct regular maintenance and inspections of all system components. This includes checking for signs of wear and tear, loose or damaged parts, and proper alignment of belts and rollers. Regular maintenance can help identify potential issues before they turn into safety hazards.
2. Use Reliable and High-Quality Components: Investing in reliable and high-quality conveyor components is crucial for ensuring safety in a cotton mill or gin environment. Quality components are less likely to fail or malfunction, reducing the risk of accidents and injuries. Choosing components from reputable manufacturers can give you peace of mind knowing that your conveyor system is built to last.
3. Provide Proper Training: Proper training for employees who work with or around conveyor systems is essential for maintaining a safe work environment. Training should include information on how to operate the conveyor system safely, how to identify potential hazards, and what to do in case of an emergency. Regular refresher training sessions can help reinforce safe practices and procedures.
4. Implement Safety Protocols: Having clear safety protocols in place is critical for preventing accidents and injuries in a cotton mill or gin environment. Safety protocols should outline procedures for emergency stops, lockout/tagout procedures, and proper handling of materials on the conveyor system. Adhering to safety protocols can help prevent accidents and promote a culture of safety in the workplace.
5. Conduct Risk Assessments: Conducting regular risk assessments of the conveyor system can help identify potential hazards and areas of improvement. By assessing the risks associated with each component of the conveyor system, you can implement targeted safety measures to mitigate those risks and ensure a safe working environment for all employees.
Summary
Improving safety standards with reliable conveyor components is essential for creating a safe work environment in facilities such as cotton mills and gins. By following best practices for conveyor component safety, including regular maintenance and inspections, using high-quality components, providing proper training, implementing safety protocols, and conducting risk assessments, you can help reduce the risk of accidents and injuries in the workplace. Prioritizing safety in the maintenance and operation of conveyor systems is key to ensuring the well-being of employees and promoting a culture of safety in the workplace.
Need Cotton Mill & Cotton Gin Components in Lubbock, TX?
Welcome to M.B. McKee Company, Inc. M.B. McKee Company, Inc. has been serving our local community of Lubbock since 1943. Locally owned and family operated, we provide great customer service and solutions for ongoing issues. With over 70 years of experience, our products, services, and engineering will always exceed your expectations. Our products include bearings, belts, chains, conveyor systems, gearing, lifts, motors, drives, product separation, tools, valves, and fittings. Our engineering division also provides general formulas, NEMA motor frames, elevator legs, screw and belt conveyors, lift charts, components from Baldor and Flexco, and various interchangeable parts. Contact us today to learn more about what we can do for you!
Categorised in: Conveyor Components
This post was written by admin